Jones Snowboards Re-Up Technology
Breathing new life into old snowboards
The quest to balance our love for snowboarding with Mother Nature’s needs has long sparked heated conversations driving brands to innovate their gear technology in pursuit of a more sustainable snowboard industry. Leading the change is Jones Snowboards, founded by legendary free-rider Jeremy Jones. At the forefront of constantly pushing for a greener future, Jones Snowboards introduces the Jones Re-Up Tech, a revolutionary technology with an increased focus on the use of recycled materials in the construction of their snowboards. This innovation not only enables snowboards to be recycled but also uses the recovered materials to produce new ones. We asked Seth Lightcap, Jones Marketing Manager, to take us through the details of their new technology and what this could mean for the future of snowboarding.
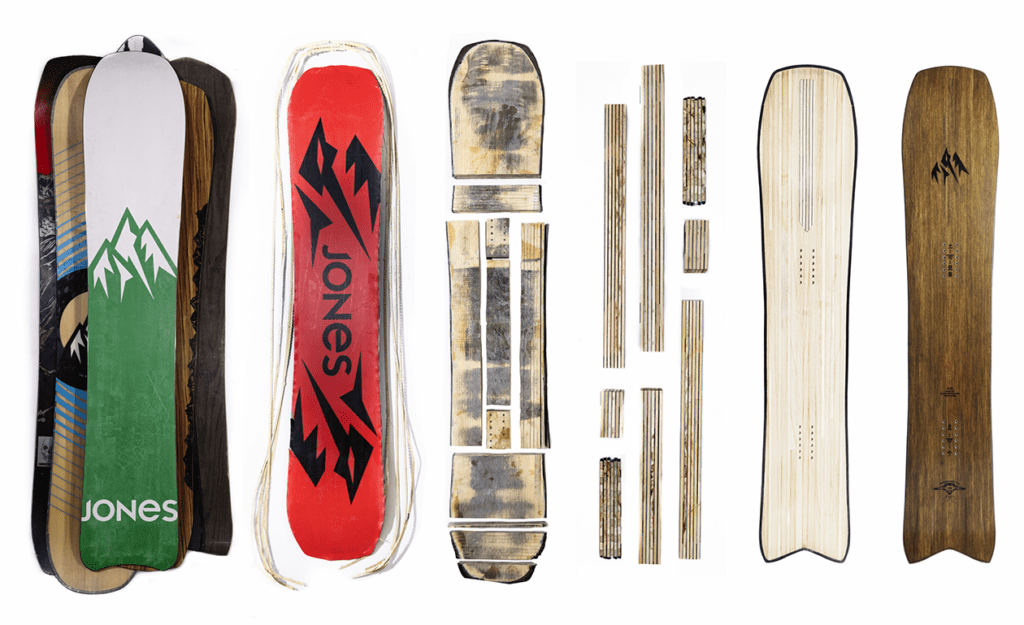
WORDS Stella Pentti
The Jones Re-UP technology sounds like a great initiative to make snowboard manufacturing more sustainable and reduce the use of virgin materials. How long have you been working on this, and where did the idea stem from?
We’ve been searching for innovative ways to recycle factory thirds and warranty boards for many years. From making skateboards to furniture, we’ve had some success with upcycling unrideable boards, but Re-Up Tech finally offers a virtually limitless outlet for using recycled snowboard materials. The development of Re-Up Tech was done in partnership with our board manufacturer, SWS Board Technology. The engineers at SWS are absolute manufacturing wizards and are always researching new ways to improve board performance and produce them more responsibly.
How much of the old board can be used to create a new board? What do you do with the remaining parts that can’t be reused?
The Re-Up Tech recycling process allows us to recycle or reuse 95% of the materials from a dead snowboard. The steel edges are removed and recycled while the majority of the snowboard is sliced up and used to make stringers for new boards. The 5% of the dead board that cannot be reused is mainly small scraps and offcuts produced when processing the board for recycling.
How does the process work? Can you take us through the recycling and upcycling steps?
Sure, so here are the four steps of the Re-Up Tech recycling process:
Step 1- Collect boards, ship them back to the factory
The Re-Up process begins by collecting warranty boards and retired boards from riders and shops around the world. The dead boards are then shipped to our factory using ocean freight. Shipping them back on a slow boat has the smallest carbon footprint possible, and we believe the benefits of recycling still outweigh this unavoidable impact.
When the retired boards arrive at the factory they begin the recycling process along with a small number of defective ‘C’ grade’ Jones boards that got rejected at some stage in the manufacturing process. The ability to recycle factory rejects is another huge benefit of Re-Up Tech.
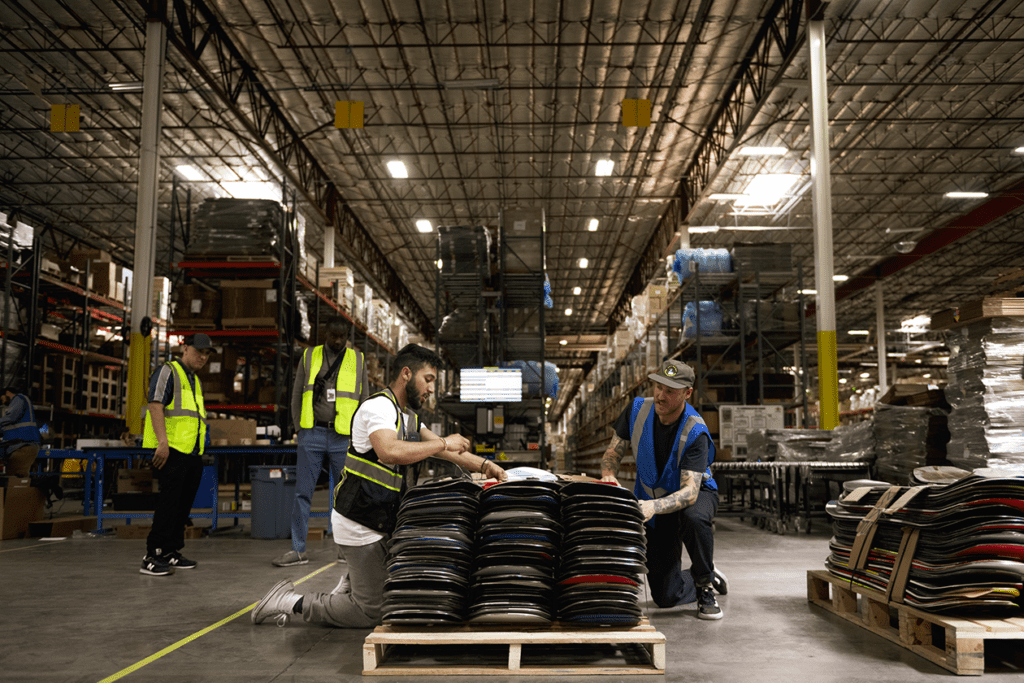
Step 2 – Prepare the boards for recycling
Once back at the factory, the recycling process begins by sanding every board’s topsheet and base to remove any dirt, wax, or solvents. The next step is to remove the steel edges and steel inserts using a mechanical process. The edges and inserts are then set aside to be recycled with other scrap steel.
Without the edges and inserts, the board is now a sandwich of P-Tex, epoxy, wood core, stringer material and topsheet. This metal-free sandwich is then flattened in a press to remove any rocker profile or 3D contours.
Step 3- Make a six board sandwich and slice it up
Six flattened boards of any brand or material composition are then stacked, glued and pressed together to create a 24 layer thick sandwich of snowboard materials. The sandwich includes six layers of P-Tex, six layers of wood core, six layers of stringers and six layers of topsheet material.
The sandwich is then cut into thin slices that include all 24 layers of recycled material. These thin slices are what gets inserted as performance stringers in the construction of new wood cores.
Step 4 — Insert the slices into new wood cores
The thin slices of recycled material are then inserted into new wood cores in the place of a traditional stringer material. Because the layers in the slice are oriented at 90 degrees relative to the word core, base and topsheet, they offer remarkable dampening and stiffening properties. In both factory and on-snow tests, these slices of compressed recycled materials proved to be some of the highest performance stiffening materials we’ve ever tested.
By using only thin slices of each recycled board, the effects of material variability are negated. It doesn’t matter if one board had a faster base + carbon stringers and another board did not. In testing, the performance of any slice, no matter its composition, is virtually identical. The recycled materials are only used in specific areas for dampening and stiffening. The majority of the wood core is made with responsibly harvested virgin wood like a traditional wood core.
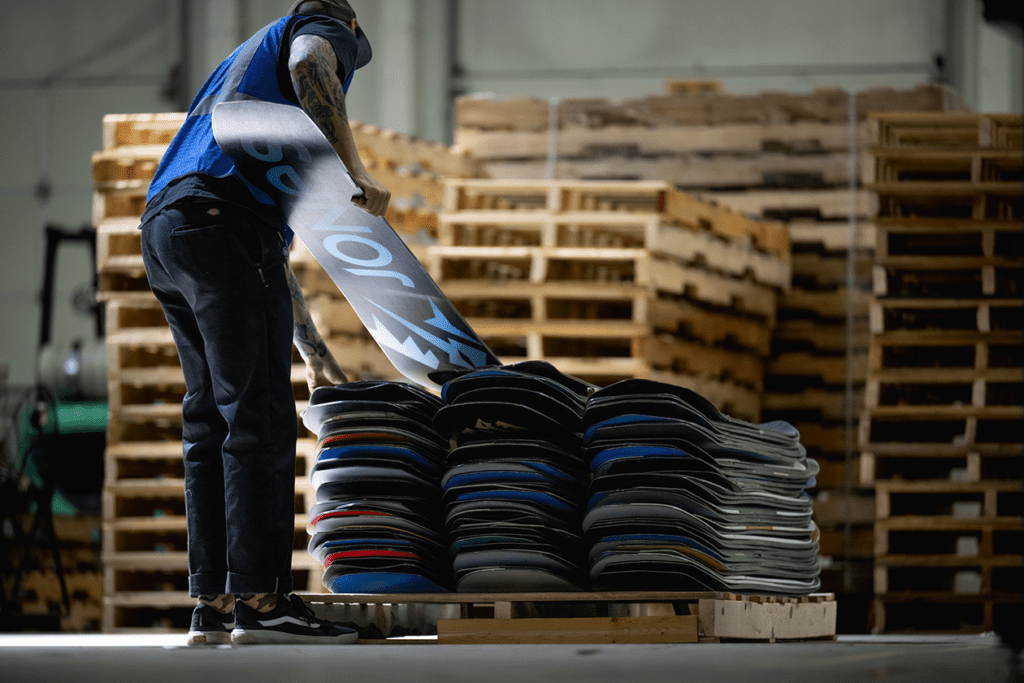
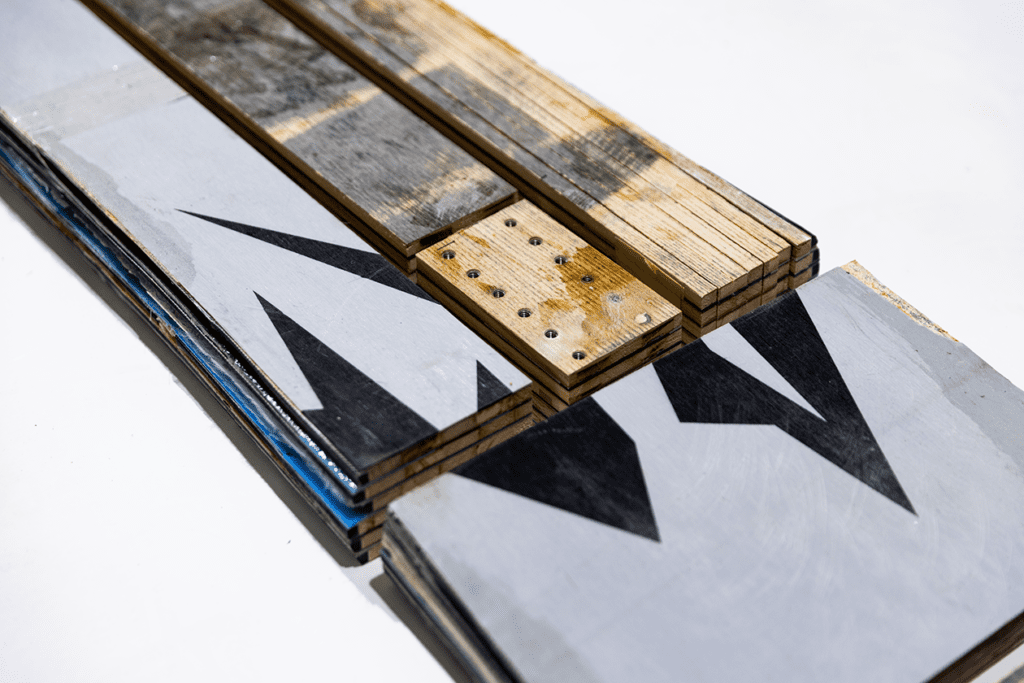
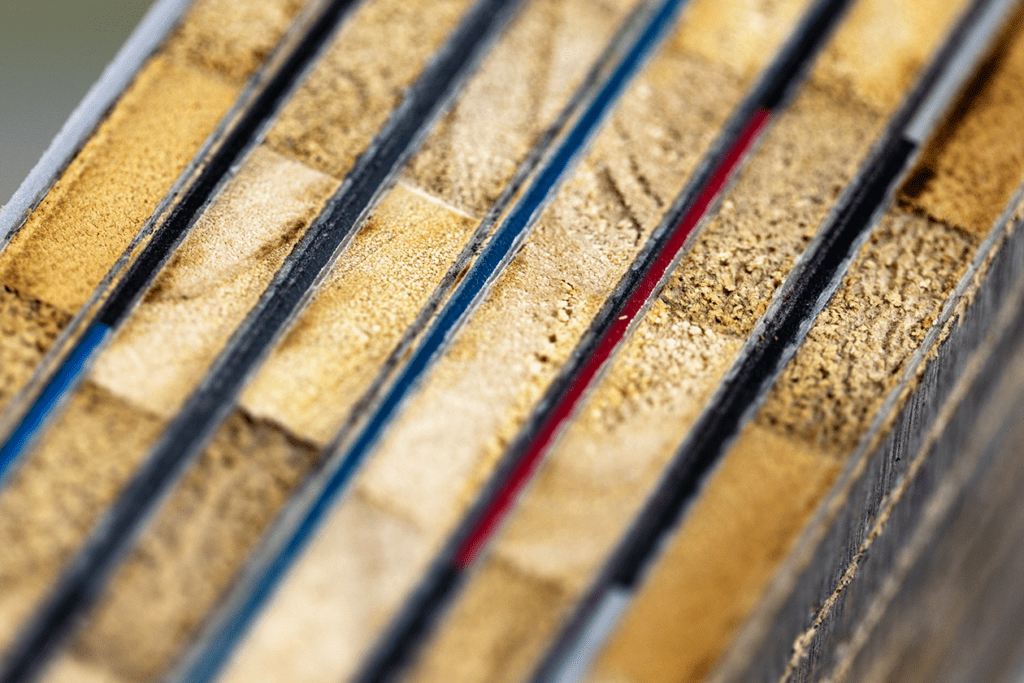
So the Re-Up technology is proving to be as good as when creating a board using virgin materials?
Yes, we use the recycled materials as stringers that get embedded in the wood cores of new boards. The stringers absorb vibrations and add pop to the board. In both on-snow and factory testing, we found that Re-Up stringers are more torsionally stable than any stringers we’ve tested.
What boards in the 24/25 collection have been produced using the Re-Up technology?
The Hovercraft 2.0 snowboard is the only board in the Jones line made with Re-Up Tech stringers for this season.
In the future, would you wish to use this for all of the Jones boards?
Our ability to introduce Re-Up Tech stringers to more boards in the Jones line hinges on the availability of dead boards to recycle. We’d love to make more models using Re-Up tech once we better establish our supply chain of unrideable boards. Last season we were able to collect 3000 boards which gave us only enough material to use in the 24/25 Hovercraft 2.0 solid.
In an ideal scenario, people get into the habit of sending their old Jones snowboards to you, and you’ll be able to start producing half of your boards using the Re-Up technology. How much would this reduce Jones’ carbon footprint per season?
As the recycling process is a brand new technology, and we’re still fine tuning our board collection network, we’re not focused on calculating what the carbon footprint savings of the Re-Up Tech project is just yet. What we do know at this point is that every board we recycle saves it from being thrown in the incinerator or the landfill which is already a huge win for both the planet and our industry.
Are there talks about implementing the Re-Up technology on products other than boards in the future?
We are always looking for new ways to make our products more responsibly and with less impact. Re-Up Tech is currently a snowboard and ski specific recycling process, but if we could create a similar technology that allowed us to recycle dead snowboard bindings or outerwear we’d be all for it.
Thank you, Seth and the Jones Snowboard family. This is very exciting news for the future of snowboarding, and we can’t wait to see what you do next.
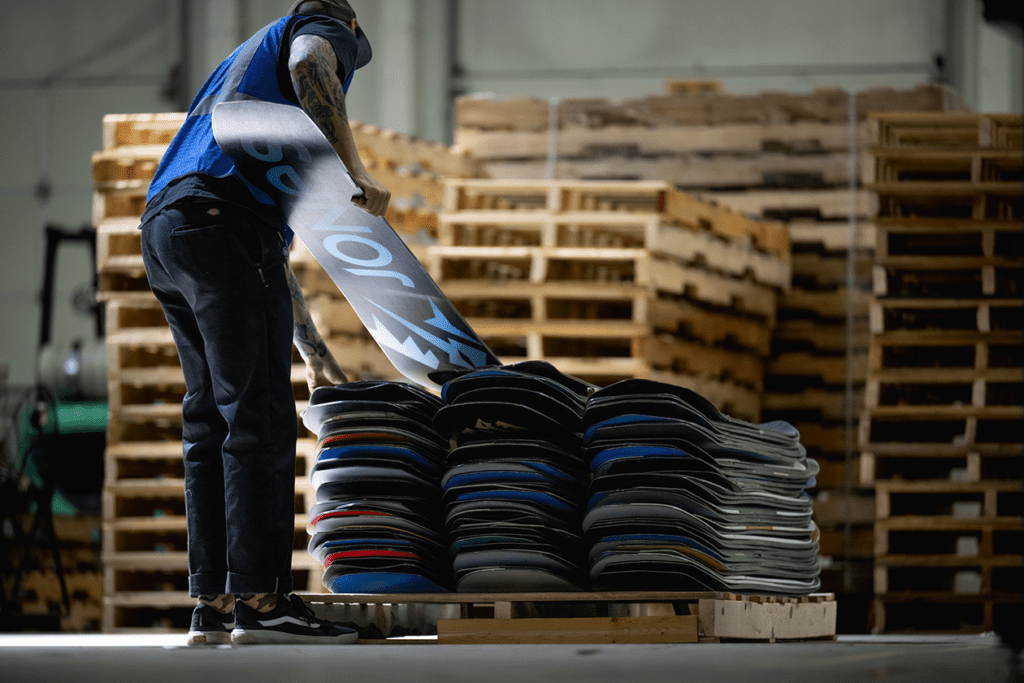